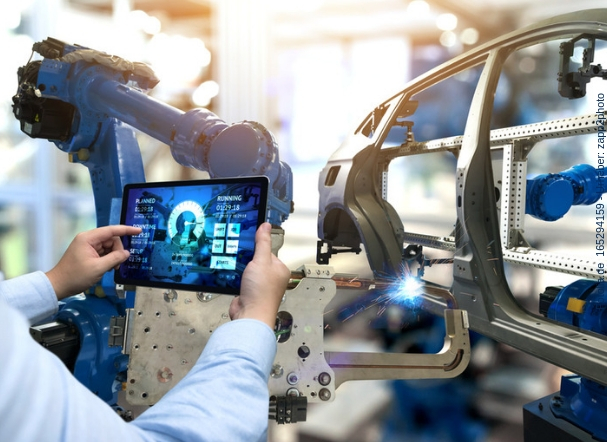
We maximize your sales
Your company is established and a permanent fixture on the market. You know your customers, distribution channels and suppliers. You have eyes on your competitors.
- But do you also know the details, your silent reserves?
- Is your production transparent?
- Do you know which workplace supplies which quantities?
- And: which he could deliver?
22 years of optimization of structural and procedural organizations have shown us:
Flexible Rationalization reduces your production costs by up to 30 percent – We help you to maximize your turnover!
The right partner at your side
Nothing is as constant as change. Every production manager is confronted with this operational fact on a daily basis. Because of that, production optimization is part of the continuous process of change. This includes four factors:
- human,
- equipment (machine),
- work object (workpiece, product) and
- information.
Without the sound analysis of the company, however, all further processes of change are on shaky ground. TUG always pursues the goal of creating reasonable, that is, rational structures, which of course have to suit the respective company. We develop key figures without which everything else is nothing. In order to grasp these, we rely on state-of-the-art technologies.
We offer you the following services
The TUG does not produce any paper that will dust your cabinets. We think and act practically. We
- analyze,
- collect the data at the workplace,
- develop with you an implementation strategy and
- control the new performance potential.
Fast, flexible and individual. We examine the basis of your company: your production. In whole or in part. Try us! The first company tour is of course free of charge for you.
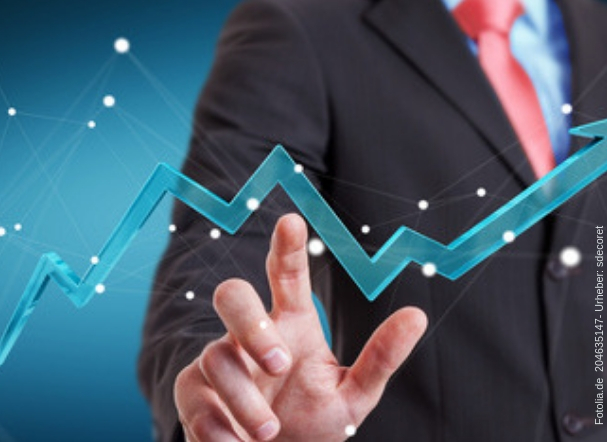
Our expertise
Be honest: Can you give us a quick overview of the quantities produced by an assembly department, a department or even your entire company per hour of employee work?
- Where exactly is this productivity index on an annual average?
- And: If you don’t know this figure exactly, what do you base your production and personnel planning on?
„TUG – Die Produktionsoptimierer“ know from many years of experience: There is no better size for capacity planning and process control. In the end, everything refers to this index: number of units per employee hour. In determining this index, malfunctions, downtimes and technical changes are always taken into account. It only has to be clearly determined.
Make your production transparent as well. Planning couldn’t be more convenient. Put your operational future on this solid foundation: number of units per employee hour – process-related utilization and flexible deployment of your employees. „TUG – Die Produktionsoptimierer“ determine this index for you, precisely documented and comprehensible.
We develop company-specific measures and guide you in the implementation of innovations.
The special steps in the project process
The basis for your success
ANALYSE
This discussion is not just about new default times, i.e. the definition of time periods, which are available for the production of a workpiece or product. Here, the product design is also put to the test:
- Which work steps are unnecessary without loss of quality?
- Which work steps are indispensable?
- Which steps have to be optimized?
We record this test bench for you using the latest technology. Because what applies to its customers applies even more to the production optimizer: Advantage through knowledge! Lifelong learning is the essential prerequisite for success.
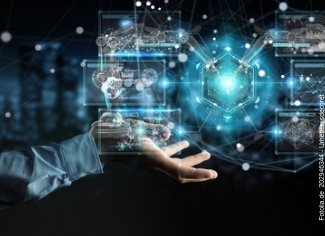
QUALITY MANAGEMENT
For time recording according to the REFA methodology and the documentation, we also rely on the latest technology and always up-to-date recording software. That’s the only way your data is safe and long-term comprehensible. It also gives you solid arguments in the necessary discussion with your workforce to initiate all necessary improvement processes. We will continue to accompany you as long as you wish.
- All data is transparent, comprehensible and ERP-compatible
- The data can be integrated into existing DIN / EN / ISO systems
Hereby we offer you an overview of our service package and introduce the most important fields of application and services.
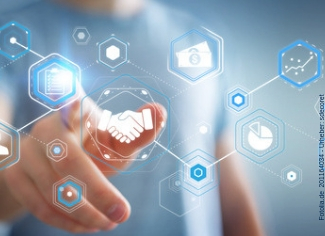
GUIDANCE
Using the most modern techniques, the steps in the route guidance previously reviewed in analysis and quality management are expanded to optimize your productivity process adapted to your company:
- rationalization process
- date fixed
- discussion of the estimated economic business benefits
These points are elaborated and documented in the route guidance in such a way that they can be optimally and efficiently implemented in the next step of the goal implementation.
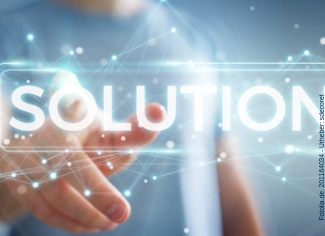
GOAL INITIATIVE
Visible results should now be achieved in the target implementation phase. This means:
- realization of the optimization process
- implementation of a new work process
- implementation of a new time plan
These conversions are intended to visibly maximize your turnover. Get to know a new workflow adapted to your company that will bring your company success.
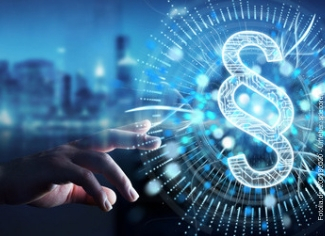
We cut your production costs by an average of 30%
Discover the potential that lies dormant in your company and make a first operational analysis completely free.
With these methods, we achieve your goals
Our approach
We help you to make your investments efficient.
Machine utilization increased by 13 percent, volume output more than doubled: these results make entrepreneurial hearts beat faster. However, an operations manager would have been denied investment success in the case of a panel sizing saw without the detective’s fine work by the project manager. TUG will therefore provide you with crystal-clear key figures and ways to increase its effectiveness, such as:
- modification of the structural and procedural organization
- key figure formation
- introduction of premium wages
- snapshots
- time studies
case study
A company had invested 150,000 euros in a new machine with the aim of increasing operational productivity. When noticeable improvements were still missing after half a year, the company turned to „TUG – Die Produktionsoptimierer“. Only a detailed analysis of all activities on the panel-sizing saw revealed what the entrepreneur had previously only vaguely noticed: The saw too often stood still.
The productive share of a day shift was only 65 percent. The rest of the time, among other things, consumed terminal operation, material removal and material supply. The fine data determined by Mr. Gastreich made the entire work process completely transparent. With such knowledge behind him, change and improvement processes can be steered in the right direction right from the start.
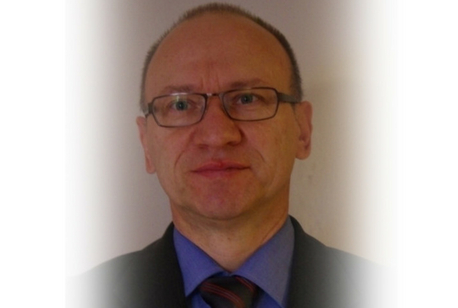
Willi Gastreich
Over 25 years of experience as a production optimizer
- REFA technical trainings
- electronics technician
- mechanic
Your contact person – Willi Gastreich
The World of Technical Management Consulting Gastreich – TUG
Willi Gastreich is the owner and your contact person of the company „TUG – Die Produktionsoptimierer“. The company is a small family business, which is specialized in the professional determination of economic ratios and the pointing out of production reserves.
He has been present on the market with increasing success since 1996. The positive development of the company in these times of accelerating change is also evidence of how much potential is still to be tapped in small and medium-sized production companies.
„TUG – Die Produktionsoptimierer“ stands for practice-oriented work. We are firmly convinced that only the knowledge of exact key figures makes a production or manufacturing unit truly transparent. Therefore we emphasise the exact determination of your production indices.
Because we know:
The more sustainable we determine, the more precisely and flexibly you can plan.
Your success is our success!